21/09/2023 Case study
Reducing energy usage during shutdown periods at Plaistow Wharf
A project to reduce energy usage when our Plaistow Wharf factory shuts down during non-manufacturing periods has generated a 44.4% reduction in energy use during these periods.
Plaistow Wharf is the home of Lyle’s Golden Syrup and was first opened by Abram Lyle in the 1880s. Today it specialises in value added speciality sugars and syrups, with more than a million tins of Lyle’s Golden Syrup leaving the factory every month.
The factory currently runs 5 days per week. Just like when we leave lights on or the TV on standby at home, we identified that more energy than necessary was being used to light, heat and cool the site, and run machinery such as compressors and fans even when the factory was not operational. Tom Davies, Process Engineer at Plaistow Wharf and the site’s sustainability lead, led a project to tackle this. Tom is responsible for improving the processes and overall efficiency of the site, including ensuring we use gas, electricity and water efficiently.
“The starting point was measuring how much energy we were actually using during shutdown periods, and then seeing how low we could get it. We turned off everything we didn’t need, and that minimum base load became the target to achieve during each shutdown.” Tom Davies, Process Engineer
Tom introduced a new shutdown procedure, including training on how to undertake it, and a digitised checklist of the machinery and equipment to be turned off accessed via a QR code on phones and tablets and submitted in real time. An investment in automated data collection software has allowed energy usage data to be collected continuously during manufacturing and non-manufacturing periods. This has helped to track performance and identify anomalies, as well as generate reports to feedback performance to individual areas and make improvements.
The project has generated an average reduction of 44% in energy usage during shutdown periods. This means that every weekend we shut down, we are saving roughly the equivalent of the annual electricity consumption of an average flat or 1 bedroom house.
Further, the project has broadened colleagues’ understanding of and commitment to sustainability.
“The reduction figures speak for themselves, but the biggest improvement has been a cultural shift and increased buy-in from colleagues to our carbon reduction commitments. By embedding energy-reducing shutdown processes in job responsibilities, colleagues now know the concrete steps they can make to reduce energy, and everyone knows how important it is to do their bit.”
Tom is now investigating how to implement the new shutdown procedure in other shutdown periods, for example when a packing line is not running, and how to shorten the amount of time it takes to shut down the factory to further reduce our energy usage. Importantly, learnings from this project at Plaistow Wharf are being shared across ASR Group to be implemented at our other factories and refineries.
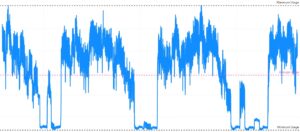